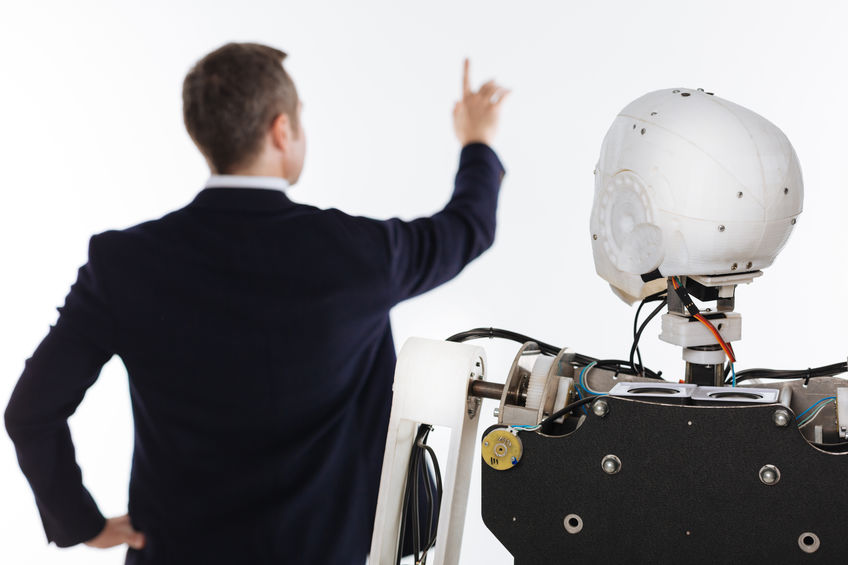
ЦИПР 2021: Четыре реальных примера от Intel, как искусственный интеллект экономит деньги и время
- 29/06/2021
- 👁 1 147 просмотров
- 0
Просто добавьте Core i7
На конференции ЦИПР 2021 (Цифровая индустрия промышленной России) об искусственном интеллекте (ИИ) говорили везде. На стендах, с трибун, во внутренних чатах. Иногда казалось, что говорящие хотят частым повторением двух слов ускорить проникновение искусственного интеллекта в производственные процессы.
А делать что-то действительно нужно, потому что сегодня лишь 11% производств в России как-то применяют ИИ. Это вдвое меньше, чем в среднем по миру (21%), и в разы меньше, чем в США (64%), ЕС (51%), Японии (51%) и Южной Корее (39%).
Но и это еще полбеды. Дело в том, что Россия «лидирует» среди отрицателей искусственного интеллекта. В странах с развитой промышленностью только 15% предприятий не хочет внедрять ИИ, ссылаясь, главным образом, на нехватку данных для внедрения в отдельных конкретных задачах и кадровый голод. В России же отрицателей целых 46%. Нехватка кадров имеет место, но куда неприятнее невозможность использования ИИ внутри имеющейся инфраструктуры предприятий и банальное отсутствие знаний о том, какая от ИИ вообще польза.
Не будем включать обвинительный тон. Искусственный интеллект – штука действительно многослойная и сложная. В ней очень мало того, что мы связываем с натуральным, органическим мышлением. И очень-очень много искусственного. Компьютер не думает, а сопоставляет данные по определенным моделям. И если сам владелец данных не очень понимает, чего хочет, то искусственный интеллект сам не догадается.
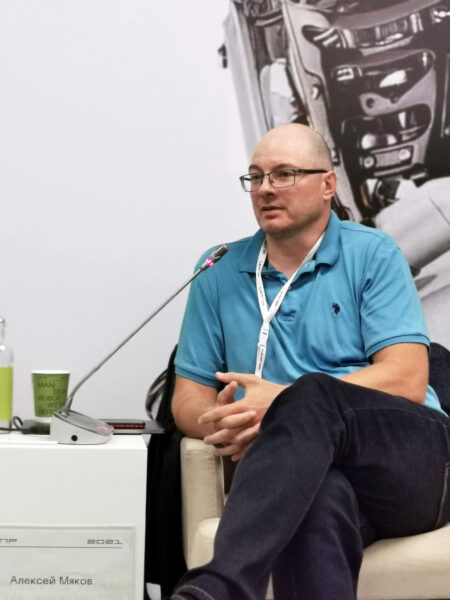
На одной из панельных дискуссий ЦИПР-2021 генеральный директор по разработкам Intel в России Алексей Мяков на ЦИПР 2021 рассказал о четырех абсолютно понятных случаях применения ИИ на производстве, давших заметный эффект.
Улучшить Audi
Завод Audi в немецком Неккарзульме собирает до тысячи автомобилей в сутки. На заводе трудится более 2500 автономных роботов. 900 из них занимаются точечной сваркой. В каждом автомобиле Audi более 5000 сварных швов. И за производственный день роботы делают свыше пяти миллионов таких швов. Для контроля качества использовался надежный, но довольно дорогой и трудный подход. Каждый день одна машина, вышедшая с конвейера, отбиралась случайным образом. Ее отвозили в специальное помещение, разбирали, и 18 инженеров со специальными ультразвуковыми инструментами проверяли каждый шов и каждую точку на нем.
Если в одной машине обнаруживались, скажем так, системные недостатки, то инженеры приступали к выборочному изучению всей партии. Но, в любом случае, выводы делались по одной машине из тысячи. И, по закону подлости, она как раз могла оказаться идеальной, в отличие от остальных 999, выпущенных в течение дня.
Intel вместе с инженерами Audi создала алгоритмы потоковой аналитики с помощью программного обеспечения Intel Industrial Edge Insights. Сопоставляя данные, полученные с контроллеров сварочных агрегатов, с накопленными результатами физически проведенных инспекций, можно сразу заметить неладное. Среди анализируемых данных напряжение на каждой газовой горелке, сила тока, конфигурация сварных швов, тип металла, уровень износа электродов и т.д. Точно зная, какое сочетание факторов ведет к проблемам, можно в будущем его просто исключить. У завода есть планы использовать наработки в других операциях. В частности, в установке заклепок, склеивании элементов и покраске.
На заводе говорят, что внедрение искусственного интеллекта уже позволило сократить затраты на оплату труда по проверке качества сварки практически вдвое. Это ни в коем случае не значит, что инженеры отправились на улицу. При нынешнем голоде на кадры они просто перешли на более интересную работу. Действительно более интересную: поверьте, нет ничего увлекательного в ежедневном обследовании сварочных точек. Ну и здорово, конечно, что теперь не надо ежедневно раскидывать по кусочкам новенькую Audi.
Поднять качество китайских автомобилей
О китайских автомобилях говорят, что с каждым годом они становятся лучше. Рассказ Алексея Мякова раскрыл некоторые причины роста качества.
На одном из крупных заводов в Поднебесной, выпускающем автомобильные двигатели, при литье деталей наблюдались повторяющиеся дефекты. Их, конечно, отлавливали наблюдательные сотрудники. Но, к сожалению, при существующих объемах производства глаз замыливался даже у самых внимательных.
На заводе был внедрен высокочувствительный алгоритм компьютерного зрения на основе искусственного интеллекта. По трем из четырех дефектов удалось добиться 100-процентного обнаружения. Четвертый компьютерный глаз засекал в 99.6% случаев, но при постановке задачи оговаривалось, что хорош любой результат от 98%.
Не менее важно, что удалось полностью исключить ложное выявление дефектов. Завод был бы доволен, если этот показатель оказался ниже 5%, но его удалось довести до 0. И теперь для монотонного контроля качества литых деталей требуется меньше людей.
Похожее решение было внедрено на другом китайском заводе, производящем автомобильные шины. Там скорость проверки одного экземпляра удалось увеличить в 10 раз при точности выявления дефектов 99.9%. Интересно, что система контроля качества работает не на каком-то мегасервере, а на вполне обычном промышленном компьютере с процессором Intel Core i7 внутри.
Ткач с искусственным интеллектом
Вряд ли я удивлю вас информацией о том, что процесс изготовления тканей давно автоматизирован. Полотна ткут машины, причем с неимоверной скоростью. Людям остается только присматривать, чтобы все шло гладко.
Но в автоматизации и скорости есть слабое место. Процесс ткачества – многопереходный, и на каждом этапе может быть заложена «основа» для будущего брака. Если вдруг нитка «заблудилась» и на ткани пошел дефект, это обнаруживается десятки и сотни метров спустя. Особенно трудно бывает заметить дефекты на ткани со сложным рисунком. Иногда в ходе отбраковки, являющейся неотъемлемой частью ткачества, вся партия идет под уценку, а то и вовсе на выброс.
Решение Intel с использованием компьютерного зрения позволило на одной из фабрик отслеживать дефекты в реальном времени. Ставилась задача достичь 80-процентного обнаружения, на практике этот показатель равен 97%. Живой человек просто физически не может достичь таких показателей. Да и жалко его.
Тысяча джинсов в минуту
Алексей Мяков рассказал еще об одной неочевидной, на первый взгляд, проблеме. На фабриках, производящих одежду, есть проблема с ее учетом. Нет, дело не в том, что сотрудники норовят унести сшитое домой. Просто у каждого наименования есть несколько размеров, плюс разные оттенки ткани, пуговицы, нашивки и т.д. и т.п. На сортировке и упаковке, конечно, стараются исключить несоответствия. Однако очень часто клиент обнаруживает при выкладке в магазине мужские джинсы среди женских, не те размеры и не совпадающие цвета комплектов.
Компьютерное зрение, натренированное на огромном количестве образцов, позволило отличать модели одежды с точностью 90%. При не идеальном освещении, в полусвернутом виде, в неудачном ракурсе – все это стало не очень важным. То есть 9 из 10 ошибок исправляются автоматически. На долю живых контроллеров остается выявление 10% пересортицы, что существенно снижает нагрузку. Заодно умная система ведет учет произведенной одежды, и на складе готовой продукции почувствовали себя увереннее.
И да, с этим тоже справляется компьютер с Core i7 с развернутым ПО Intel Industrial Edge Insights.
Итого
В свое время, когда на заводы стали приходить станки и машины, рабочие встречали их без энтузиазма. Действительно, тех, кто привык к монотонному низкоквалифицированному труду, машины лишали рабочих мест.
При нынешнем кадровом голоде такой сценарий вряд ли возможен. Число желающих делать скучное задешево падает год от года. От большинства повторяющихся механических действий человека уже почти избавили. Теперь приходит время избавления от скучной как бы интеллектуальной работы. Искусственный интеллект не выгорает и не унывает. Он готов взять на себя ответственные участки, где много ответственности, но нет места озарениям.
И это работает вот уже прямо сейчас.